How are coins and numismatic products made
Since the birth of an idea to the technology of production.
Works on a coin or numismatic product start with a brainstorming session
The making of the coin consists of a number of factors which require the involvement of many employees, including technologists and artists-medallists. The design of the project and its implementation translate into the success of the product on the numismatic market.
Accepting the project
and production of tools
In the first place, our designers create several graphical projects of a given collectible. Only when the final project is accepted by the technologists, the plaster model of a coin or a numismatic product can be created. Before sculpting the plaster, the artist prepares a positive image of the project molded in plasticine.
This is a very time-consuming stage, requiring from the sculptor up to several dozen hours of hard work and meticulous attention to detail. Both working stages – molding and sculpting of the plaster models – are processed by hand. The above mentioned method can be called a traditional one. Nowadays, 3D projects of commemorative coins can be also created with the use of a special computer programing – ArtCam.
Digitizing the design
When the positive plaster model is accepted, the image etched onto its surface is scanned with a 3D scanner. In the next step the image is reduced in size and transferred to the electrode. Finally, an iron mold is carved based on the digital file.
Stamping tools (bearing a negative image) are polished by hand, chrome-plated and hardened in otfrt to enhance their quality and durability. However, 3D images created in ArtCam program are transferred directly to the electrode without need of scanning the plaster.
Flawless
When minting tools are ready, and the images are transferred to the electrode, the minters of the Mennica Polska start preparing the blanks. Commemorative coins are most frequently struck on gold and silver blanks.
To make its surface mirror-like and shining, the blanks are hand-polished or immersed in a metal ball bath. Distilled water and chemicals are poured into the ball swirl. After a long bath the surface of the blanks is flawless and shining, what ensures a high collector value of the proof coins.
Minting
Now the coin billets and stamps are ready for the minting process. Both circulation and commemorative coins are struck under the supervision of a machine operator. Minting presses strike up to 750 circulation coins per minute!
However, when we talk about manufacturing collector products, the capacity of the machinery is much lower. Striking commemorative coins is time-consuming due to their complex designs and diversity of decorations applied on their surface. One strike is sufficient for minting a circulation coin, but for collector coins, multiple strikes are used.
Quality check
New coins fall into a trap for inspection after which they are conveyed to get counted, weighed and bagged for shipment. The quality of both coins and numismatic products is monitored at several stages of the production process, starting from the graphic design, ending with the packaging of finished products.
All coins are accompanied by technical specifications. Above this, Mennica Polska has introduced strict restrictions on access to the production facilities. Personal control is obligatory before entering selected rooms.
See also
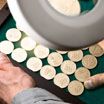
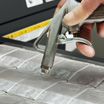
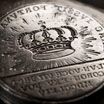